Die wahren Kosten von Ausfallzeiten können für Unternehmen zeitraubend und kostspielig sein. Ungeplante Ausfallzeiten sind teuer, aber die meisten Einrichtungen sind sich vielleicht nicht bewusst, wie viel sie ihr Unternehmen genau kosten. Die folgenden Abbildungen verdeutlichen die wahren Kosten von Ausfallzeiten.
Nahaufnahme einer Person, die Geräte in einer Fertigungsanlage repariert
Wie viele Ausfallzeiten entstehen in Unternehmen?
Die Anzahl der jährlichen Ausfallzeiten in Unternehmen ist ziemlich hoch, wie unten dargestellt:
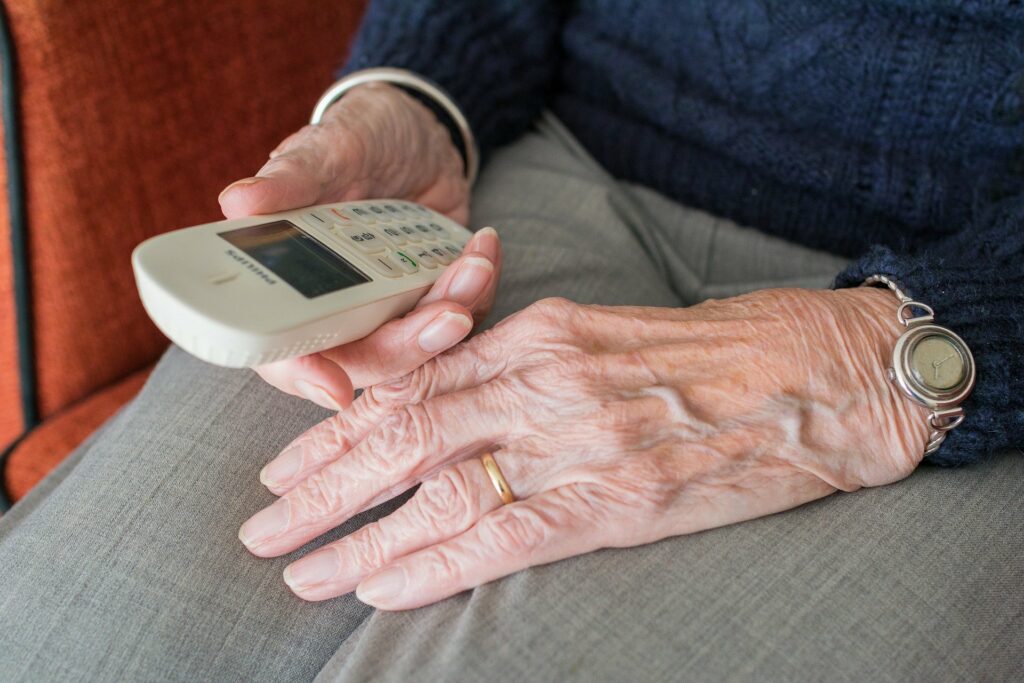
Auch in der Pflege (siehe Pflegedienst Stuttgart) spielt dass eine wichtige Rolle. Sollten sie einen Pflegedienst Köln suchen, dann melden Sie sich!
Insgesamt 82 % der Unternehmen haben laut einer Studie in den letzten Jahren ungeplante Ausfallzeiten erlebt.
Im Durchschnitt können diese Ausfallzeiten mindestens vier Stunden dauern.
Konkret können Hersteller bis zu 800 Stunden Ausfallzeit pro Jahr verzeichnen.
Wie viel kostet jede Stunde Ausfallzeit?
Bei den großen Mengen an Ausfallzeiten, mit denen Unternehmen konfrontiert sind, stapeln sich die Kosten:
Im Jahr 2016 beliefen sich die durchschnittlichen Kosten für Ausfallzeiten pro Stunde über alle Unternehmen hinweg auf 260.000 US-Dollar.
IT-Netzwerkausfallzeiten belaufen sich im Durchschnitt auf 300.000 US-Dollar pro Stunde oder 5.600 US-Dollar pro Minute.
In der Automobilindustrie sind die Kosten mit 22.000 Dollar pro Minute außergewöhnlich hoch – über 1,3 Millionen Dollar pro Stunde!
Was ist der Grund für die Kosten von Ausfallzeiten?
Die Kosten für Anlagenstillstände ergeben sich aus der Art und Weise, wie ausgefallene Anlagen die Produktivität des Unternehmens beeinträchtigen:
Fast die Hälfte aller Unternehmen, bei denen es zu Ausfallzeiten kommt (46 % ), sind infolgedessen nicht in der Lage, ihren Kunden Dienstleistungen zu liefern.
Etwa 37 % verlieren Produktionszeit für eine kritische Anlage, und 29 % der Unternehmen sind nicht in der Lage, bestimmte Anlagen zu warten.
Fabriken verlieren in der Regel mindestens 5 % ihrer Gesamtproduktivität aufgrund von Ausfallzeiten.
Wie können Hersteller ungeplante Ausfallzeiten reduzieren?
Was tun Unternehmen angesichts der Produktivitätsverluste durch Ausfallzeiten, um unerwartete Ausfälle von Anlagen zu reduzieren? In vielen Fällen nicht viel, wie unten gezeigt:
Leider sind etwa 80 % der Betriebe nicht in der Lage, ihre Ausfallzeiten genau zu berechnen.
Weniger als ein Viertel der Maschinenbetreiber (24 %) nutzen prädiktive Analysen, die anderen verwenden stattdessen reaktive oder zeitbasierte vorbeugende Wartung.
Dennoch sind prädiktive Methoden mit dem geringsten Prozentsatz ungeplanter Ausfallzeiten verbunden – 5,42 % aller ungeplanten Ausfallzeiten im Vergleich zu 8,43 % bei reaktiver und 7,96 % bei geplanter Wartung.
Um die Ausfallzeiten von Anlagen zu reduzieren, müssen die Einrichtungen anfangen, präzisere Methoden zur Diagnose von Problemen mit ihren Anlagen zu verwenden. Prädiktive Analysen und eine sorgfältige Wartungsplanung können die Betriebszeit von Anlagen verbessern und Ihren Wartungsteams Zeit und Geld sparen.
Was verursacht Ausfallzeiten?
Was die Ursachen für Ausfallzeiten angeht, gibt es einige bemerkenswerte Faktoren. In vielen Fällen liegt es an defekten Anlagen.
Im Jahr 2018 verursachten veraltete Anlagen etwa 44 % aller ungeplanten Ausfallzeiten.
Bedienerfehler und Zeitmangel waren mit 16 % bzw. 15 % weitere Ursachen für ungeplante Ausfallzeiten.
Neben neuen Technologien und verbesserten Wartungspraktiken sind der Umgang mit veralteten Anlagen und die Verbesserung von Schulungen der Schlüssel zur Reduzierung von Ausfallkosten.
Tipps zur Reduzierung von Ausfallzeiten
Wenn man sich die wahren Kosten von Ausfallzeiten ansieht, wird deutlich, wie wichtig es ist, diese Kosten auf ein Minimum zu reduzieren. Aber wo fangen Sie an? Die folgenden Tipps können Ihnen helfen, Ausfallzeiten in Ihrer Anlage zu reduzieren.
Tipp: Die Verwendung eines CMMS kann Ihnen helfen, viele der unten aufgeführten Tipps umzusetzen.
- Schulen Sie Ihr Personal
Da ein erheblicher Teil der ungeplanten Ausfallzeiten auf Bedienerfehler zurückzuführen ist, ist es ein Schritt in die richtige Richtung, wenn Sie sich die Zeit nehmen, Ihre Mitarbeiter zu schulen bzw. zu schulen, um Ausfallzeiten zu reduzieren.
Die meisten Bediener und Wartungsmitarbeiter müssen eine Vielzahl von Anlagentypen, Diagnosegeräten und Steuerungssystemen im Auge behalten. Wenn Sie also sicherstellen, dass sie sich mit allen gut auskennen, können Sie Bedienerfehler vermeiden und Arbeitsaufgaben beschleunigen, auch solche, die dazu dienen, die Anlagen in gutem Zustand zu halten.
Tipp: Die Hersteller der von Ihnen verwendeten Geräte sind mit Sicherheit gerne bereit, Nachschulungen für ihre Geräte anzubieten.
- Analysieren Sie Ihre Risiken
Eine Risikobewertung ist der Schlüssel zur Vermeidung von Ausfallzeiten, da Sie so wissen, wo Ihre Risiken liegen und wie Sie diese am besten angehen können. Auf diese Weise können Sie Ihre Bemühungen auf die wichtigsten Probleme konzentrieren, anstatt einen Schrotflinten-Ansatz für das Facility Management zu wählen.
Ein Werkzeug zur Risikobewertung ist die Fehlermöglichkeits- und Einflussanalyse (FMEA). Bei der FMEA werden potenzielle Fehlermodi und ihre möglichen Auswirkungen in Bezug auf Prozessausfallzeiten, Sicherheitsrisiken, Reparaturzeiten usw. untersucht.
Einige der Risiken, die Sie analysieren sollten, sind:
Sicherheit
Umwelt
Produktionsausfall
Anlagenkosten, einschließlich der Kosten für die Wartung
Während Sie jeden Fall untersuchen, ordnen Sie jedem eine Risikoprioritätszahl (RPZ) zu, basierend auf der Schwere und Wahrscheinlichkeit des Fehlermodus. Auf diese Weise können Sie Ihre Bemühungen besser auf die Vermeidung der wichtigsten Fehlermodi konzentrieren.
- Konzentrieren Sie sich auf proaktive Wartungsstrategien
Wenn Ihre Anlage derzeit einen „Feuerlösch“-Ansatz bei der Wartung verfolgt, werden Sie höchstwahrscheinlich von einer proaktiveren Sichtweise profitieren. Proaktive Wartungstaktiken wie präventive Wartung (PM) und vorausschauende Analysen reduzieren die Ausfallzeiten von Anlagen, indem sie kleinere Probleme beheben, bevor sie sich zu größeren Ausfällen entwickeln.
Der grundlegendste Ansatz für eine proaktive Wartung ist die vorbeugende Wartung. Diese Aufgaben umfassen regelmäßige Tune-ups, Schmierung, Austausch von Verschleißteilen und Inspektionen. Es kann einige Zeit dauern, bis Ihre Mannschaft von einem reaktiven zu einem proaktiven Ansatz wechselt, daher sind konsequentes Training und Wartungsplanung der Schlüssel.
Es kann hilfreich sein, mit nur einer Anlage in Ihrer Einrichtung zu beginnen. Wählen Sie eine Anlage aus, die Ihnen risikoreich erscheint, und schauen Sie, welche Arten von Ausfällen am häufigsten auftreten. Bestimmen Sie, welche PM-Aufgaben diese Ausfälle verhindern würden, und setzen Sie sie in die regelmäßige Praxis um. Wenn Ihr Team diese Aufgaben durchführt – und darüber Bericht erstattet -, können Sie die Auswirkungen Ihrer vorbeugenden Instandhaltung erkennen und bei Bedarf Anpassungen vornehmen.
Sobald Sie die vorbeugende Instandhaltung für eine Ihrer Anlagen gemeistert haben, führen Sie sie auf andere Anlagen aus und bauen sie von dort aus auf. Mit der Zeit wird Ihre Mannschaft den Dreh raus haben und die proaktive Wartung zu einem selbstverständlichen Teil Ihres Facility Managements machen.
- Implementieren Sie vorausschauende Analytik
Wenn Sie bereits ein präventives Wartungsprogramm eingeführt haben, ist es vielleicht an der Zeit, auf eine vorausschauende Wartung (Predictive Maintenance, PdM) umzustellen. Die vorausschauende Wartung nutzt IIoT-Elemente wie Sensoren, die Daten von Ihren Anlagen sammeln, z. B. deren Temperatur oder Vibrationen.
Diese Daten werden von Analysesoftware verarbeitet, die Daten protokolliert und Trends verfolgt. Wenn etwas signifikant von den etablierten Trends abweicht und auf einen potenziellen Fehler in der Anlage hinweist, wird ein Arbeitsauftrag ausgelöst. Fortgeschrittene Analysesysteme können sogar die Art der erforderlichen Wartungsarbeiten vorschreiben und so potenziell Zeit für Diagnosetests einsparen.
Es hat sich gezeigt, dass PdM zu erheblichen Kosteneinsparungen gegenüber der Instandhaltung führt, die oft Aufgaben umfasst, die keine wirklichen Probleme beheben. Mit Predictive Analytics sind Sie in der Lage, die Wartungsaufgaben auf die tatsächlich vorhandenen Probleme zu konzentrieren.
Um mit PdM zu beginnen, folgen Sie einem ähnlichen Prozess wie bei der Instandhaltung: Wählen Sie eine Anlage, statten Sie sie mit einigen kostengünstigen Sensoren aus und überwachen Sie die Daten. Wenn sich die Daten signifikant von den normalen Trends unterscheiden, ist das Ihr Stichwort, um sie zu überprüfen. Mit der Zeit werden Sie ein ausgefeilteres automatisches System aufbauen wollen.
- Nutzen Sie Ihre Daten
Wenn Sie Daten von Anlagensensoren, Arbeitsaufträgen und ähnlichem sammeln, stellen Sie sicher, dass Sie diese Daten auch nutzen. Manchmal investieren Einrichtungen Tausende von Dollar in ausgefallene Geräte und nutzen die gesammelten Daten kaum, was letztlich den Zweck ihrer ursprünglichen Investition zunichte macht.
Die Daten müssen in die Wartungsplanung und die Arbeitsabläufe integriert werden, um wirklich effektiv zu sein. Eine Möglichkeit, dies zu tun, besteht darin, sie durch ein CMMS und eine Datenvisualisierungssoftware besser zugänglich zu machen. Wenn die Daten aus Ihren Instandhaltungsprozessen durch Softwarelösungen verfügbar gemacht werden, wird Ihr Team sie bei der Erstellung von Arbeitsaufträgen und Wartungsplänen für jede Anlage mit größerer Wahrscheinlichkeit berücksichtigen.
- Optimieren Sie aktuelle PM-Praktiken
Nicht jede Lösung für Ausfallzeiten beinhaltet notwendigerweise fortschrittliche Technologie (was eine gute Nachricht für kleinere Unternehmen mit begrenzten Ressourcen ist). Darüber hinaus sind nicht alle Ausfallzeiten ungeplant. Geplante Ausfallzeiten können auch eine Belastung sein, besonders wenn sie für unnötige Aufgaben verwendet werden.
Oft ist eine Optimierung der laufenden vorbeugenden Wartungsaufgaben erforderlich, insbesondere wenn man bedenkt, dass 30 % der Wartungsaktivitäten zu häufig durchgeführt werden. Die Aufgaben, die Sie für Ihre Anlage geplant haben, sind vielleicht nicht unbedingt notwendig.
Der Schlüssel zur Optimierung der vorbeugenden Wartung ist, das zu tun, was funktioniert, und weniger von dem zu tun, was nicht funktioniert. Die Verfolgung von Wartungsdaten ist für diesen Prozess von entscheidender Bedeutung. Wenn eine bestimmte Aufgabe keinen Einfluss auf den Zustand Ihrer Anlage zu haben scheint, ist es wahrscheinlich an der Zeit, sie zu reduzieren. Dies bedeutet, dass weniger Zeit für Wartungsarbeiten benötigt wird und somit weniger unnötig geplante Ausfallzeiten.
- Optimieren Sie die Wartungsabläufe
Neben der Optimierung der vorbeugenden Wartung ist es auch wichtig, sicherzustellen, dass Ihre Wartungsabläufe im Allgemeinen so schlank sind, wie sie nur sein können. Das bedeutet, alle Formen von Verschwendung zu vermeiden, wie z. B:
Wartezeiten
Falsch eingesetzte oder nicht ausgelastete Mitarbeiter
Transport
Schlechtes Bestandsmanagement
Unnötige Wege von einem Bereich der Anlage zu einem anderen
Diese Formen der Verschwendung können reduziert werden, indem Sie einen Blick auf Ihre Wartungsabläufe werfen und sehen, welche Hindernisse auftauchen könnten. Ihre Arbeitsauftragsdaten können in diesem Fall hilfreich sein, insbesondere wenn es um die Gesamtzeit für die Durchführung jeder Wartungsaufgabe geht. Darüber hinaus kann es aufschlussreich sein, Ihre Techniker einfach zu beobachten, um zu sehen, wie ihr Tag aussieht.
Ihr Wartungsplaner sollte bei der Erstellung von Arbeitsaufträgen für Ihre Techniker Dinge wie den Standort der Anlage, benötigte Betriebsmittel und Materialien sowie die Zugänglichkeit der Geräte berücksichtigen. Die Bereitstellung von Anlagenschemata und Wartungschecklisten für Ihre Crew über mobilen Zugriff kann ebenfalls Zeit sparen.
Tipp: 5S ist ein Prozess, der Ihnen helfen soll, diese Art von Verschwendung zu reduzieren und Ihre Anlage insgesamt effizienter zu machen. Durch Sortieren, Ordnen und so weiter können Sie Ihre Wartungsabläufe optimieren.
- Organisieren Sie Ihren MRO-Bestand
Ein gut organisiertes MRO-Inventar ist der Schlüssel zur Effizienz Ihres Wartungsteams, daher sollten Sie sicherstellen, dass es so effektiv wie möglich gehandhabt wird.
Auch wenn Sie die Menge Ihres Inventars einschränken müssen – schließlich verursacht es Kosten – ist es absolut wichtig, dass Sie die richtigen Ersatzteile in ausreichender Menge vorrätig haben, um Ausfälle von Anlagen schnell beheben zu können. Andernfalls müssen Sie möglicherweise auf eine Ersatzteilbestellung warten, bevor Sie die ausgefallene Anlage reparieren können.
Wie in den meisten Betrieben gibt es auch in Ihrem Unternehmen eine Vielzahl von Marken verschiedener Anbieter, die Sie im Auge behalten müssen.
Eine solide MRO-Bestandsverwaltung ist besonders wichtig, wenn Sie alte und veraltete Geräte in einem funktionsfähigen Zustand halten müssen. Die Teile, die Sie benötigen, können schwierig oder teuer zu beschaffen sein, und das kann wochenlange Wartezeiten bedeuten. Daher sollte Ihre Bestandsmanagementstrategie angemessene Vorlaufzeiten für die Beschaffung schwer zu ersetzender Teile vorsehen.
- Sichern Sie Ihre Systeme
Softwaresysteme, insbesondere ältere, sollten für den Fall eines Ausfalls Ihres IT-Netzwerks gesichert werden. SPS, SCADA und andere Steuersysteme (ganz zu schweigen von anderen Softwaretypen) halten Ihre Anlage am Laufen, und wenn Sie sie nach einem Ausfall nicht wieder in Betrieb nehmen können, kann dies Stunden oder sogar Wochen Produktionsausfall bedeuten.
Ältere Systeme sind besonders wichtig zu sichern, da sie schwieriger zu ersetzen sind. Wenn das Unternehmen, das Ihnen Ihre aktuellen Steuerungssysteme zur Verfügung gestellt hat, nicht mehr im Geschäft ist, kann das bedeuten, dass Sie Ihr System wochenlang von Grund auf neu programmieren müssen.
- Aktualisieren Sie alte Geräte
Viele Einrichtungen verlassen sich auf veraltete Maschinen und Anlagen. Auch wenn diese Geräte größtenteils noch funktionieren, stellen sie ein Risiko dar, wenn sie ausfallen – und ältere Geräte neigen dazu, häufiger auszufallen als neuere Maschinen. Reparaturen an älteren Anlagen können teuer und schwierig sein und es könnte bedeuten, dass Sie versuchen müssen, Teile von weit entfernten Standorten zu beschaffen.
Wenn Ihre älteren Anlagen mit neueren Teilen nachgerüstet werden können, können Sie Zeit und Geld sparen, indem Sie die Ausfallzeit im Falle eines Ausfalls verringern. Auf lange Sicht ist die Anlage auch weniger störanfällig, was die Ausfallkosten weiter reduziert.
Auch ein kompletter Austausch kann nicht ausgeschlossen werden. Die Kosteneinsparungen in Bezug auf Energie und Zuverlässigkeit können sich durchaus lohnen.
- Verbessern Sie die Kommunikation
Ihre Wartungs- und Betriebsmannschaften werden nur so gut funktionieren wie die Kommunikationslinien innerhalb ihrer Abteilungen. Die Mitarbeiter müssen wissen, wohin sie gehen sollen, was sie tun sollen und wie sie es tun sollen. Darüber hinaus kann die Kommunikation Ihrer Ziele dazu beitragen, die Akzeptanz neuer Richtlinien und Verfahren zu fördern.
Darüber hinaus ist auch die Kommunikation Ihrer Mitarbeiter mit ihren Vorgesetzten wichtig. Sie verfügen in der Regel über ein solides Erfahrungswissen darüber, was in der Praxis vor sich geht, und dieses Wissen kann für Entscheidungsprozesse entscheidend sein.
Schließlich ist die Kommunikation zwischen den Abteilungen – insbesondere zwischen Wartung und Betrieb – der Schlüssel zur Vermeidung von Arbeitsverzögerungen. Wenn Ihr Wartungsteam beispielsweise auf eine Maschine zugreifen muss und die Betriebsabteilung davon nichts weiß, kann die Arbeit zusätzliche Zeit in Anspruch nehmen.
Fazit
Ausfallzeiten können für Hersteller und andere Industrien verheerende Kosten verursachen, was bedeutet, dass Ihre Bemühungen, diese zu reduzieren, gezielt und effektiv sein müssen. Eine Kombination von Strategien, die auf Ihre Anlage zugeschnitten sind, kann Ihnen helfen, Ausfallzeiten auf ein Minimum zu beschränken und die Zuverlässigkeit zu erhöhen.